top of page


Engineering Consulting: Paint and Coating
Paint Formulation and Materials
Coatings are multi-component systems. There are constitute from a binder, pigment, additive and carrier fluids. Each elements contribute to shape the paint properties.
1.1 Pigment:
Commonly a colorant, used for its optical/aesthetic properties. The pigments give color and opacity to the coating. Pigments can be natural or synthetic, organic or inorganic. Size and crystal form of the pigment depends from its process preparation and its nature.
High temperature pigments – optical coating
Several black complex metal oxide pigments are commonly used in coil coatings.
These include copper chromite black (C.I. Pigment Black 28), manganese ferrite black (C.I. Pigment Black 26), chrome iron nickel black (C.I. Pigment Black 30), and iron chromium oxide (C.I. Pigment Green 17, Brown 29, Brown 35,).
1.2 Binder:
The function of binder is to give protection to the substrate and to the components within the film. Binder strongly influences the key properties such as gloss, durability, flexibility and toughness. The binder is made of one or more basic resin or polymer systems, either synthetic or natural resin systems. Typical types of binders include polyesters, polyurethanes, acrylics, polyesters, silicates, epoxies, oils, melamine resins, depending upon the substrate and cured performance required. The selection of the binder constitutes the major portion of the coating system. The selection is generally govern by the characters of the coating. For solar coating, the selection will be based on its: - Temperature resistance. - Adhesion to the substrate (metal, glass…) - Resistance to the environment conditions (high percent of humidity, salt, dust, wind…). The choice of the binder optimizes: - Film formation - Durability of the coating (weather resistance, chemical resistance) - Physical properties (flexibility and hardness). At high temperature applications, binders in used are generally silicones resins who have a high heat resistance.
1.3 Additives:
Fillers are used to fill the paint, maybe to thicken the film, support its structure or to simply increase the volume of the paint. Additives provide a wide range of modifications to the composition of the film and film properties. They are usually added in only small amounts. Examples include additives to: - Modify surface tension - Improve flow properties - Improve the finished appearance - Improve paint stability to UV - Reduce foaming - Slow down reaction time - Improve adhesion - Flatten -matt finish - To give nonstick surface to the paint film - Improve corrosion resistance Fillers are usually made of cheap and inert materials, such as talcs. Not all paints include fillers, other quite large percentages. With some paints, the filler provides important functional properties in the cured film, materials such as Zinc or Aluminium loading as high as 50% by volume is used to give corrosion protection capabilities to the paint film by been sacrificial to the ferrous substrate. These are a key part of corrosion protection capability.
1.4 Carrier Fluids:
Solvent or liquid carriers are used to assist in the application of the paint, it typically reduces the viscosity of the binder /pigment /filler /additive mix to allow the material to be applied via dip or spray. Once on the substrate, the solvent will evaporate, leaving the film. The term liquid carrier is considered more appropriate as it may not be a true solvent for the binder, but acts as a carrier. This may be water or an organic solvent. This component however is optional, as some paints do not require thinning for application.
2. Paint Formulation
2.1 Dispersing process
The dispersion of a pigment in liquid coatings, paints or inks to produce stable suspension, can be divided into the following three processes:
2.2 Pigment wetting
The air or water covering the pigment is substituted by the resins or dispersing agent and wetting agents.
2. 3 Grinding stage
The grinding process can be regarded as a de-flocculation process.
2.4 Grinding tools
3. Order of addition
The usual way of incorporation of dispersant in a coating formulation would be in three stages :
1 -Mix the dispersant in the millbase solvent or in the resin/solvent mixture
2 - Add any other additives
3 -Add the pigment, in stages, and disperse in the normal manner .
What is a good dispersion?
Every pigment particle is completely: – Deflocculated –
Enveloped by a layer of binder or solvent. – In practice, this is difficult to achieve.
– Important to keep the percentage of oversized pigment agglomerate as low as possible
3.1 Selection of materials
– What to think?
1- What is the metal temperature during the application? Will the equipment be shut –down (ambient) or in operation (hot).
2- What type of steel are you coating: carbon, austenic or stainless?
3- Which high temperature primers should I select for use in atmospheric exposure?
4- Has the surface been coating previously painted?
5-What are your dry time parameters?
6- What are your cure capabilities?
7-What are the federal, state and local VOC regulations requiring you to use?
8-What are your color requirements for the project? 9-Coating application method
10 – Thickness of the coating…
3.2 Adhesion
• Adhesion of a coating (paint, adhesive) to the substrate is a critical property determining its quality, durability and aesthetic properties.
Strong adhesion is achieved by a combination of the surface treatment including cleaning (degreasing), mechanical or chemical roughening and increasing the substrate wettability.
– Cleaning
– Surface roughening
– Primers
– Adhesion promoters
– Plasma treatment





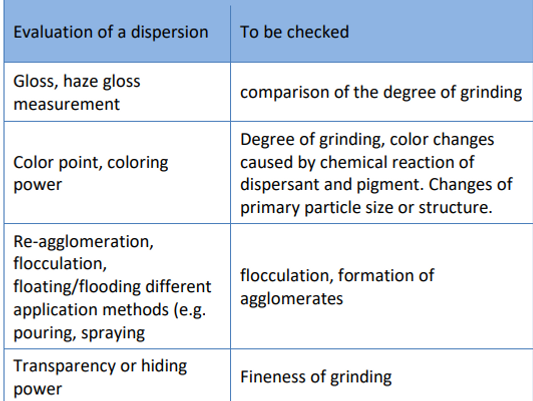
Paint and Coating: Text
bottom of page